RTU is the core unit of SCADA system to implement the measurement and control of oil Wells, water source Wells and booster pump stations. It is an intelligent remote terminal to realize the real-time collection, storage, alarm and control of the production process data of the above three kinds of measurement and control objects, and meets the application requirements of production sites such as oil Wells, water source Wells and booster pump stations. The design of the standardized digital oilfield RTU is designed according to the application of the field environment and the complex electrical environment, which can meet the various needs of the oilfield and the harsh natural environment and electrical environment. At the same time, the design of the RTU can meet the realization requirements of the intelligent function of the digital oilfield. According to the design concept of standardization and template, the standardized RTU can meet the field application requirements of oil Wells, water source Wells and booster pump stations through simple parameter configuration.
Station RTU Controller Of Measurement And Control Of Oil Well
Product Description
Station RTU Controller Of Measurement And Control Of Oil Well Features:
Here is the acquisition simulation device. Multiple acquisition analog devices can be collected through the 816AI extension module cascade, and other use modes can be customized. The introduction is as follows:
1. Data acquisition mode of RTU: three modes of RTU expansion interface (default mode), wireless ZigBee network and RS485 wired fieldbus network;
2. Start and stop control mode of RTU: control the start and stop of oil well through the DO interface of RTU;
3. RTU to frequency converter adjustment: through RTU RS485 interface (Modbus RTU protocol);
4. RTU frequency modulation (oil well regulation): it can be realized through DO interface of RTU or RS485 interface of RTU (Modbus RTU protocol);
5. RTU reads the electrical / electric energy data: read the electrical / electrical energy data of the multi-function meter through the RS485 interface (Modbus RTU protocol) of RTU;
6. RTU reads the map data: RTU supports the following map acquisition modes (other modes can be customized);
Wireless load displacement integrated sensor mode;
Wireless load sensor + wireless angular displacement sensor mode;
Wireless load sensor + wireless dead point switch + wireless cable displacement mode;
7. Data sampling mode of RTU: the sampling period of schematic diagram data can be set;
8. The default communication mode between the RTU and the monitoring center is to use the Ethernet interface of the RTU and communicate with the monitoring center through the computer network of optical fiber / wireless network (other customizable)
Technical index of SM40P-5800 RTU
project | explain |
processor | 32-bit microprocessor with a main frequency of 500 MHz |
memorizer | DDR SDRAM 128MB; Flash 256MB standard, up to 512MB |
source | AC 180V ~265V |
back up power | DC 24V |
6-way analog quantity input (AI) | 16bits sampling accuracy;Input 4~20mA, with over-voltage and overcurrent protection;Pt 100 temperature sensor interface |
12-way digital quantity input (DI) | Passive dry node, the device internal power supply is 24V |
10-way digital volume output (DO) | Relay output, capacity of 5A / 250VAC, 5A / 30VDC |
3-way RS485 | Modbus RTU Master Agreement |
1-way RS232 | Modbus RTU slave Agreement |
1-way Ethernet RJ 45 | Modbus TCP or IEC60870-5-104 protocol |
1. Route of 2.4G ZigBee communication interface | ZigBee PRO 2007 Standard |
Watch dog, real-time calendar clock | The Calendar clock loses power for 3 months |
working temperature | -40℃~+70℃ |
Storage temperature | -55℃~+85℃ |
relative humidity | 5%~95% without condensation |
weight | 0.48Kg |
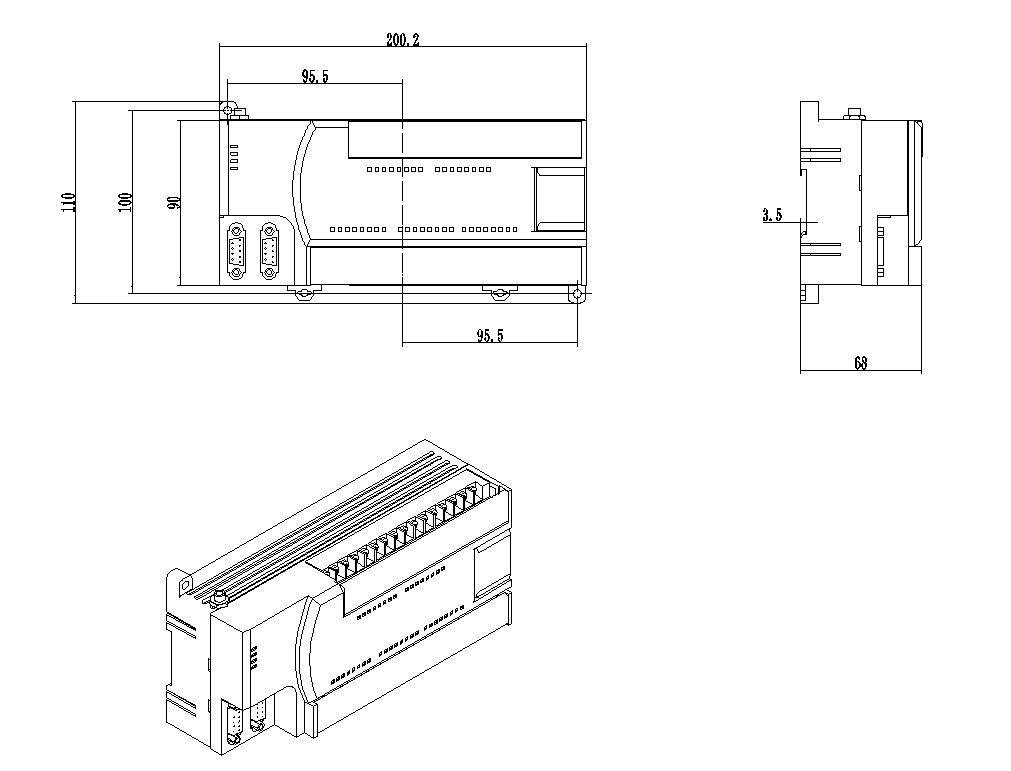
Tags
Get In Touch With Us !
Related Products
Related Productspartner
partner